
Consumer Reports: Best American Made Appliances
The thousands of products that pass through Consumer Reports test labs each year come from all corners of the globe. There are washing machines and water heaters from Mexico, TVs and refrigerators from South Korea, dishwashers and vacuums from…
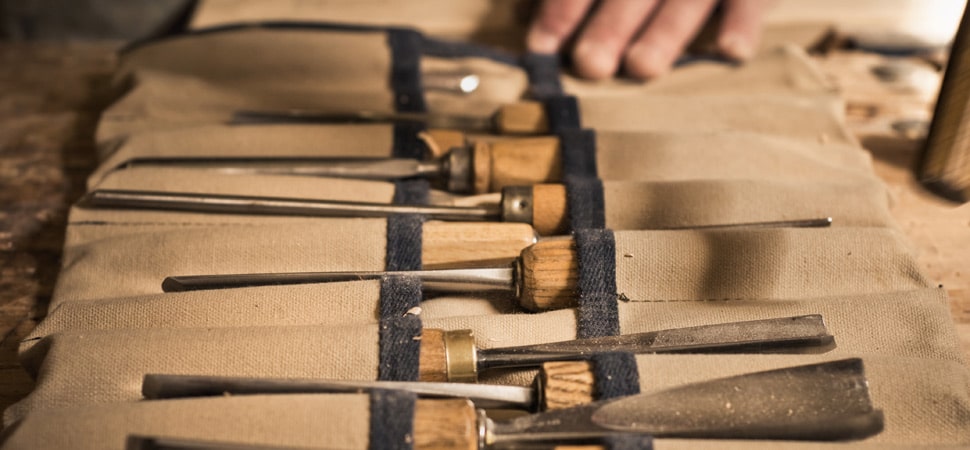
The American Flag: Made in USA and Creating Jobs in the Process
The American flag flapping above the McBattas Packaging and Printing building on the north edge of town is unremarkable as flags go.
At 3-by-5-feet, it’s not especially large. Its colors, of course, are the standard red, white and blue, and…
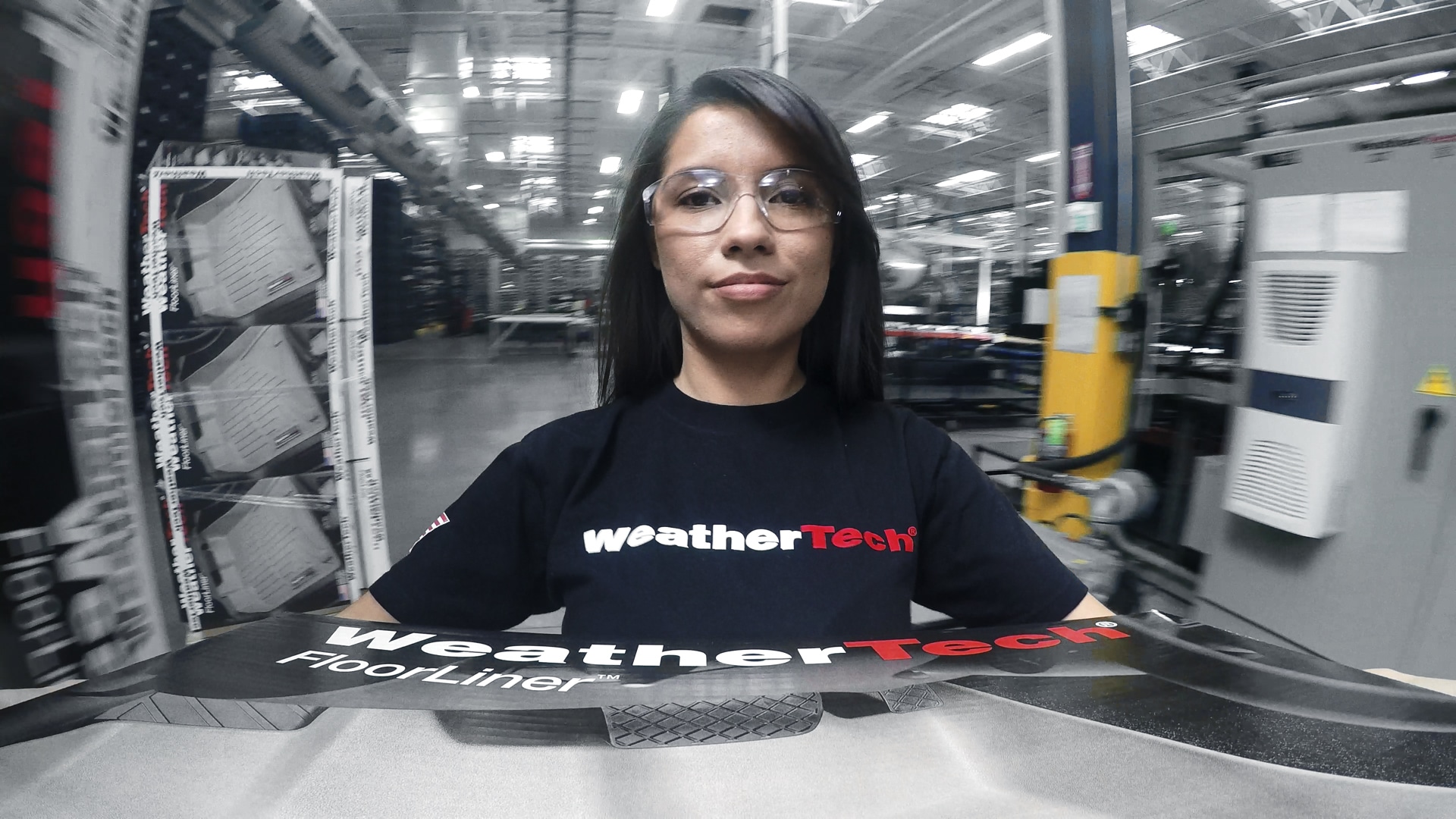
WeatherTech Fleshes Out Made-In-USA Message During Super Bowl
WeatherTech aired its second consecutive Super Bowl advertisement Sunday, picking up on the same made-in-America theme that the company hatched in its first Big Game ad a year ago.
“There’s something happening right here in this…
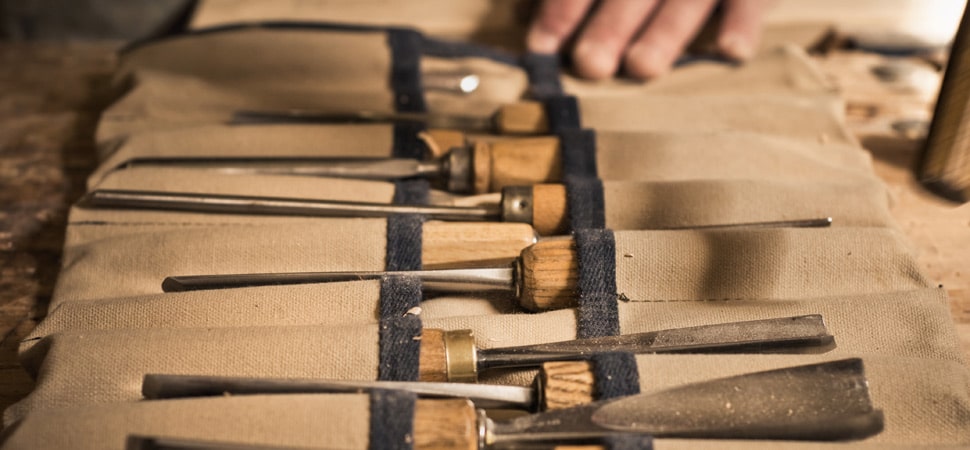
The Case for ‘Made in America’
It's about pride in what we do, not about protectionism. BY MARK DWIGHT
The Case for 'Made in America'
I proudly add the "Made in USA" label to every product I manufacture in my San Francisco factory. Making bags in this country is fundamentally…
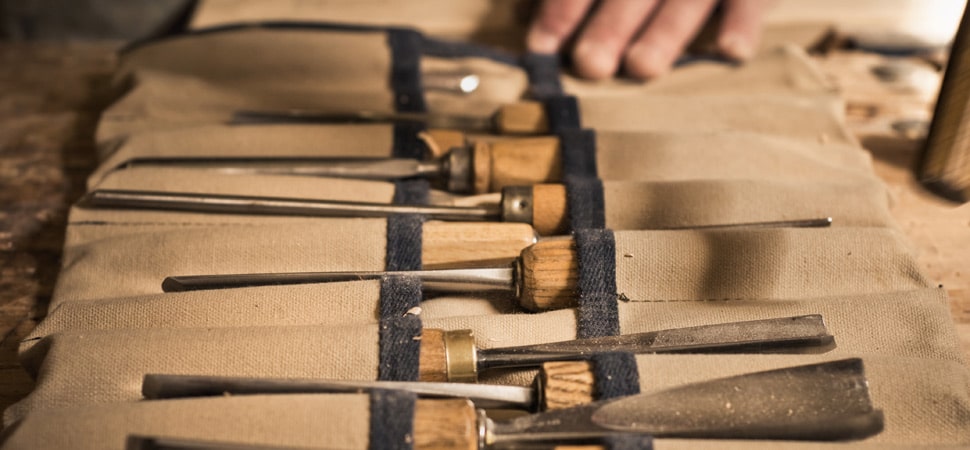
Maker’s Mark Accused of False Advertising
Two California consumers sued one of Kentucky's best-known distilleries, saying Maker's Mark tries to spike demand and sticker prices by falsely promoting and advertising its bourbon as being handmade.
The lawsuit, filed in federal court…
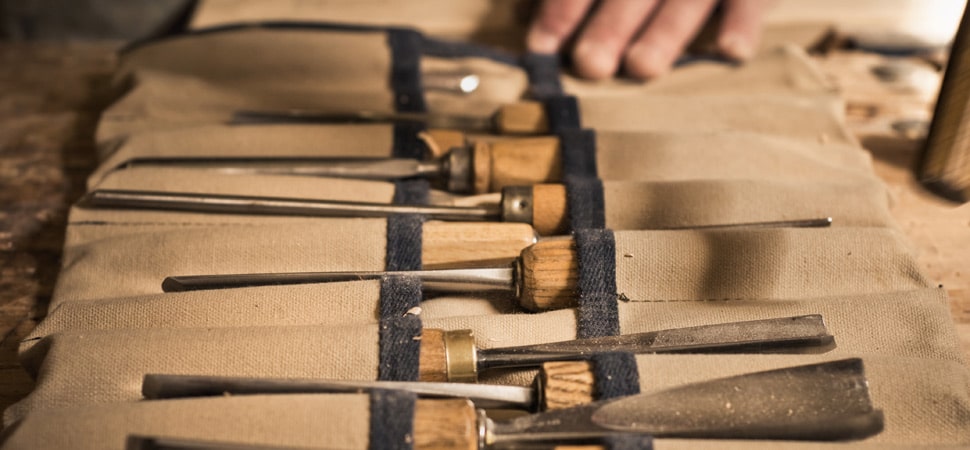
Give American This Season
It's time for America's annual holiday study of contrasts.
First comes Thanksgiving, a heritage slightly scarred by glitzy parades, football, turkey fryer incidents, and overeating, but still imbued with volunteerism, thankfulness, and…
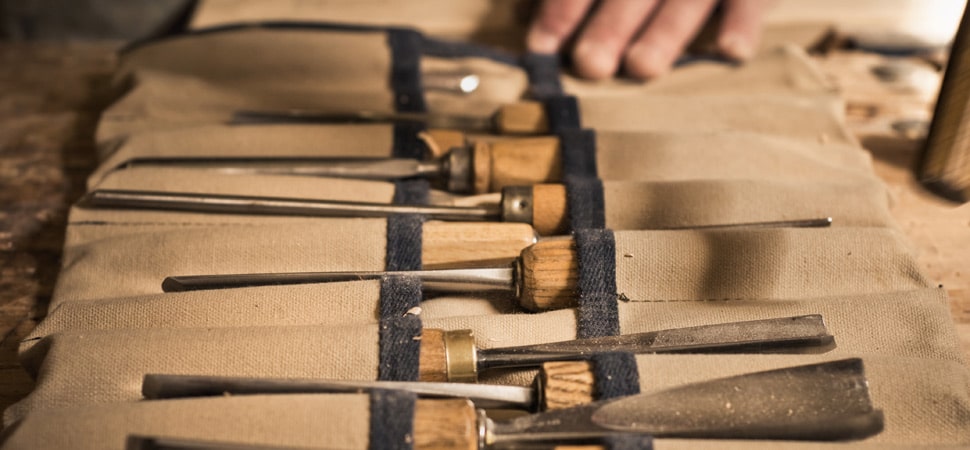
Thankful for a Made in USA Thanksgiving
by Alliance for American Manufacturing
Get to the stores before it's all gobbled up.
Halloween is over and Christmas is starting to creep onto our televisions and into our grocery stores, but don’t be confused by the pumpkin to peppermint…
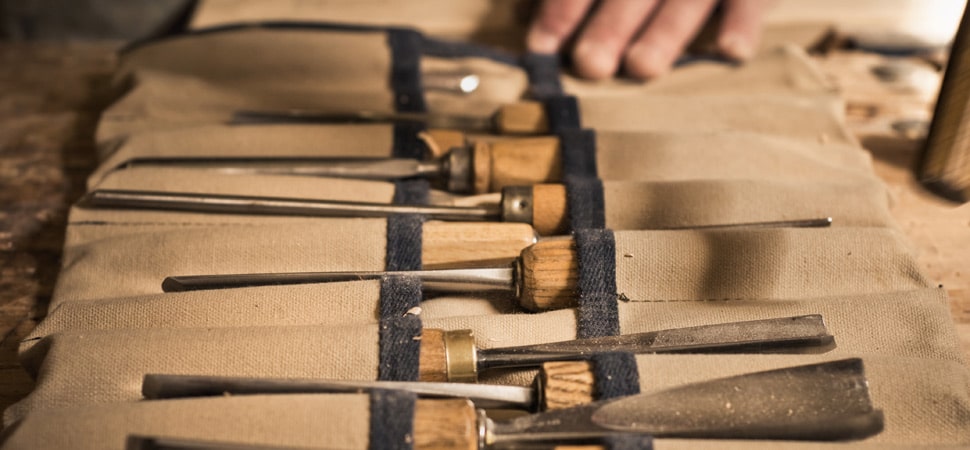
Ford Adding 850 New Jobs To Build 2015 F-150
Ford Adding 850 New Jobs To Build 2015 F-150. Ford announced today it will add 850 new jobs in Dearborn to build the all-new 2015 F-150 pickup that is the automaker's most advanced pickup in 66 years.
The new hires will be sprinkled…
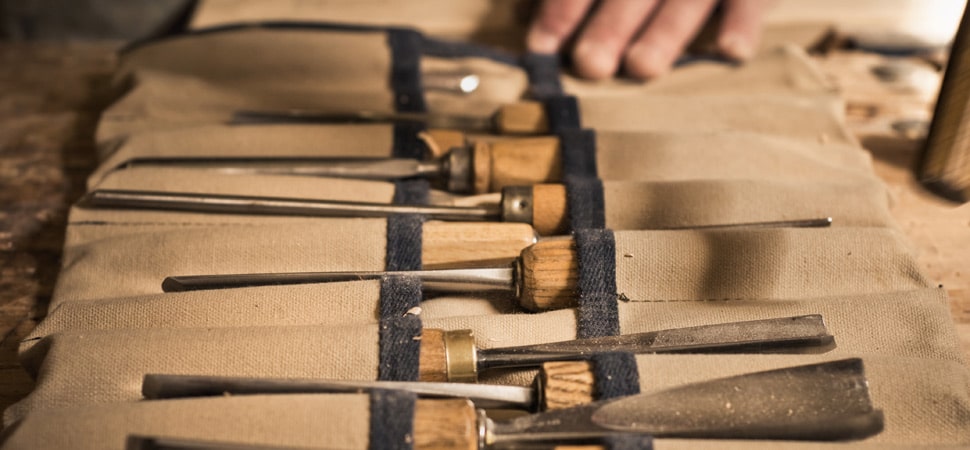
Made in America: Why American Giant Didn’t Want to Build Factories in China
American Giant: Made in America.
With the prevalence of outsourcing factory work to Bangladesh and China, fewer retailers can use those three short words on popular clothing.
Three years into its existence, American Giant is sticking…
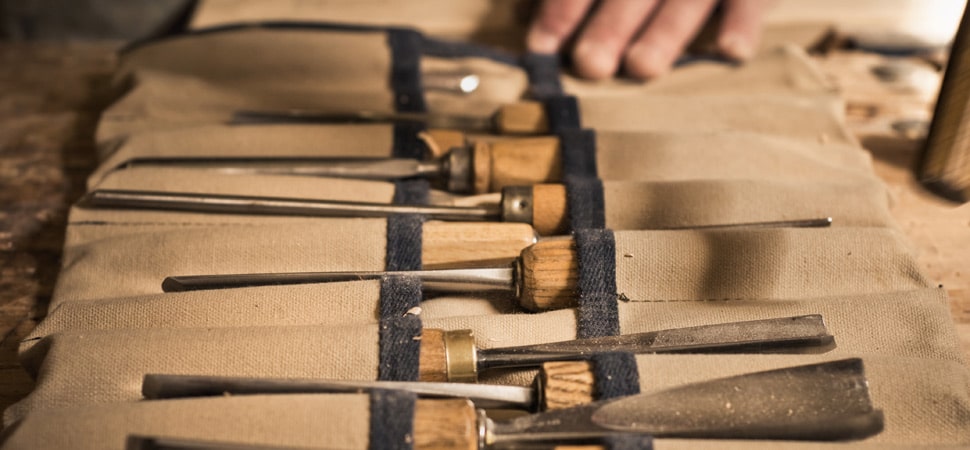
Tesla Finds Home in Nevada
CARSON CITY, Nev. (AP) — Tesla finds home in Nevada! Gov. Brian Sandoval announced Thursday that Nevada won a high-stakes battle with four other states for Tesla Motors' coveted battery factory, but the win comes with a hefty price tag…